Forklift Speed Limits and Braking in the Warehouse
Forklift instability is one of the most common causes of injury among forklift accidents in the workplace. Forklifts can tip or overturn when the driver accelerates or brakes too quickly. In particular, when a forklift is travelling around a corner or down a slope, it is very easy for a forklift to roll sideways or tip forwards or backwards from incorrect use of the brakes or accelerator.
This post will help to outline key aspects to consider when controlling speed and safe brake distances in your warehouse, making it a safer place for not only forklift drivers but pedestrians as well.
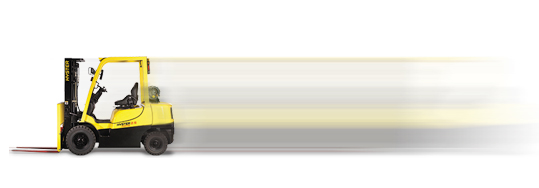
Forklift Limitations
Forklift drivers are often not fully aware of the limitations of their forklift. As a result, many forklifts are pushed close to their stability limitations.
It is important that the supplier of the forklift ensures that forklift operators are aware of the limitations of the forklift they will be driving. Forklift operators cannot simply rely on applying the right amount of brake force in an emergency stop, without causing the forklift to become unstable.
For forklift drivers and surrounding pedestrians to remain safe in the workplace; forklift drivers must be informed of all speed limits applicable in their workplace, the stability limits when braking and any factors in the environment that may affect these.
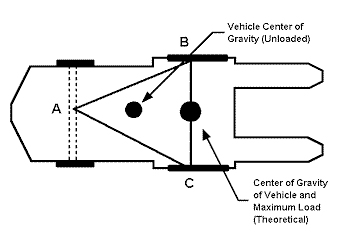
Speed control
Employers must place tight controls on transportation. There are numerous ways to control speed and ensure safer transport in the workplace:
• Ensure that workplace speed limits match environment conditions, such as, the flow of pedestrians, any corners or areas that can cause poor vision, lighting conditions as well as the type and weight of the load being transported.
• Implement speed limiting devices and make them compulsory to all forklift drivers in the workplace. These devices can reduce the maximum speed of a forklift depending on the load weight, height and turning radius.
• Post clearly visible speed limit signs around the workplace; reminding drivers of their limits and enforcing those speed limits.
• Remove any motivation for their forklift drivers to speed.
• Create pedestrian exclusion zones based around the maximum speed travelled in the warehouse and the types of loads being carried by the forklifts.
• Purchase speedometers for each forklift. These devices can be made to signal warning alarm’s when the speed limits are exceeded increasing a drivers awareness.
• Reduce speed limits in a warehouse to pedestrian walking speed; especially in high traffic areas and poor vision spaces.
• Implement GPS & RFID zoned speed limiting control (create speed limits in different zoned areas such as racking warehouse, pedestrian crossing & outside speed).
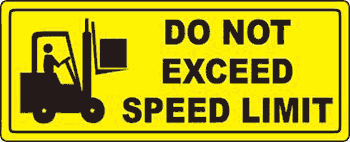
Braking control
Another important aspect of speed limitations is safe braking distances which must be considered when planning out any forklift travel paths in the workplace.
Safe braking distances are determined by many factors and are often largely underestimated in emergency situations. It is important for all forklift drivers to be trained and knowledgeable on how long it takes for their forklift to stop when travelling at different speeds.
When considering safe braking distances employers need to take into account other factors that affect these safe distances. Here are a few things that need to be considered:
• A forklift travelling at 6km/per hour usually requires around 3 meters to come to a safe stop. This is more than double with a forklift travelling at 12km/per hour. You can see these statistics displayed in the Work safe (2006) table below.
• The weight and size of a load will affect how quickly a forklift can stop in an emergency. A loaded forklift cannot be expected to stop at its maximum capabilities as the load itself can cause the forklift to tip or slide.
• Has the forklift been properly maintained? What are the tyres and brake conditions like? If a tyre is old and worn down it will not grip to the ground, therefore taking longer to stop the forklift once the brakes are applied.
• Uneven surfaces, uphill/downhill slopes and slippery ground conditions can also greatly increase the amount of time it takes for a forklift to come to a standstill.
Forklift operators need to be aware of not only the environment they are operating in, but the condition of their forklift in order to avoid tipping or overturning. Employers must take into account any factors that will risk the safety of their forklift operators and put into place safety mechanisms to counteract them.