Effects of Mass Customisation on Manufacturing
Over the past few decades there has been an emerging trend in manufacturing known as mass customisation. Mass customisation is a concept whereby the customer has a much higher involvement in the manufacturing process, being able to specify the features of the product that they want, for example, selecting the functional and aesthetic features of cars. Essentially, this trend reflects a change in manufacturers’ attitudes. They are now listening to what the market and consumers are demanding and addressing these requirements. As Australia is a high cost environment, this is becoming an ever-present characteristic of manufacturing firms as more and more companies accept that they cannot match the outputs of rival nations.
This blog covers key aspects of mass customisation in regards to manufacturing, from changing attitudes, though to disadvantages and advantages.
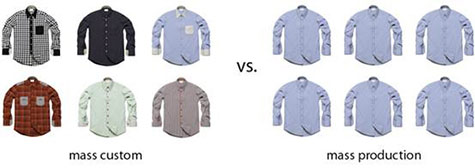
How Attitudes Have Changed
For centuries, manufacturing has been predominately about producing as much of a certain product at the lowest unit cost in order to create value for the manufacturer, better known as mass production. As a result, this production-centric approach has told the customer what they need, leaving very little scope for input from the consumer. In essence, mass customisation is a response to consumers demand for far greater control over the features of products that they wish to buy. For countries where cost of labour is high, such as Australia, this is looking a more and more attractive proposition and one which many companies have already adopted.
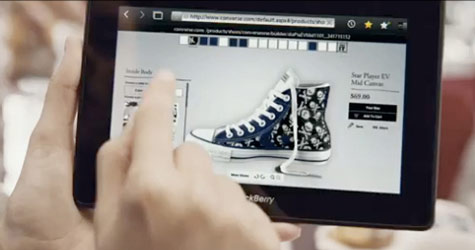
Adopting a Mass Customisation Approach
Embracing mass customisation does not happen without stringent planning and a vast understanding of its principles, especially if you are coming from a mass production background. The most important facets that a business can have are agility and a better understanding of supply chains in order to meet the customer’s specific needs and still manufacture efficiently. In addition to this, incorporating effective customer-centric design and being more flexible are key to economically customising a company’s product offerings and producing them efficiently.
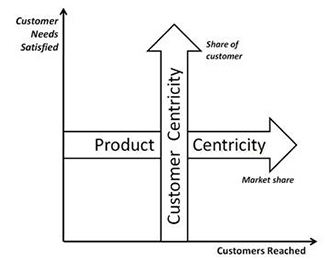
Advantages
• Customers are often more pleased with the finished product they receive, as it’s to their specification.
• Your workforce is more fulfilled as they now partake in numerous tasks as opposed to one production line responsibility.
• Customised products are more attractive to consumers than uniform products.
• Companies can forge strong relationships with their customers. That loyalty leads to return business time and again.
• As nothing is produced until an order is received, there are huge savings to be made by eradicating inventories of unsold goods and raw materials.
Disadvantages
• Maintaining a high level and variety of stock can incur high warehousing costs. Large amounts of capital are also tied up in stock.
• Typically, as the products are custom made they have a higher cost.
• Offering mass customisation with mass production efficiency is very difficult to achieve.
• If you are coming from a mass production background it is extremely tough to change your organisational structure and culture.
• Substantial investment is needed in information technology to create close integration between all links of your organisation’s value chain and external suppliers and intermediaries.
Best Practices
Due to the high costs of labour within Australia, employing mass production alone as an approach to manufacturing is a thing of the past for many. Firstly, for any business starting up or transitioning to a different approach, identifying demand is crucial.
An effective route that many companies are taking is initiating collaborations with other firms. Creating a network of companies that each specialise in specific tasks working in an integrated fashion to share equipment and capabilities can ease the pressure on your company as you initially come to grips with mass customisation and meeting the demand and expectations of your customers. However, this necessitates smart information sharing technologies.
Firms are also employing technologies to help them meet demand for a wide range of products such as additive manufacturing, assistive automation and flexible scalable intelligent processing.
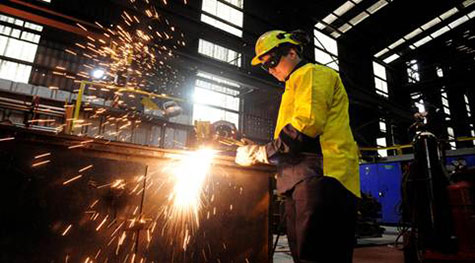
One thing that all firms can do without incurring heavy costs is gaining a better understanding of supply chains, smarter collaboration and partnerships and increasing agility in how your firm can customise its offerings to meet customer needs. Addressing all these aspects will ensure your manufacturing efficiency is high as it can be without employing specialist technologies.
Reference: Mak, S (June 2013) Will mass customisation change Australia’s manufacturing future? Rala Multi Communication Specialists