How To Conduct A Proper Tyne Inspection
This week’s blog is part two in our series looking at proper tyne care and maintenance. Following on from our previous blog providing an introduction into tyne care and maintenance, this blog will look at how a proper tyne inspection should be carried out. The post will provide detail on seven critical elements of a pair of tynes that need inspection.
Under Australian standard ANSI/ITSDF B-56.1 (2012):
“Tynes in use shall be inspected at intervals of not more than 12 months (for single shift operations) or whenever any defect or permanent deformation is detected. Severe applications will require more frequent inspections”
Tyne inspections should be conducted by a trained person and any tyne found to be showing any form of defect should be immediately removed from service and shall not be returned unless it has been satisfactorily repaired or replaced.
The recommended tool to use for tyne inspections are a set of fork calipers, which act as a go/no-go gauge.
As part of a tyne inspection there are seven elements that need to be closely looked at:
1. Surface Cracks
Tynes need to be thoroughly examined for any signs of visual cracking, sometimes it may be necessary to utilise non-destructive crack detection methods if cracks are not visible to the naked eye. Special attention must be paid to the heel, welds and any mounting device attaching the tynes to the forklifts carriage. If surface cracks are detected tynes must be removed from service immediately.
If surface cracks go undetected they may deteriorate further overtime and eventually break, which could lead to serious injury, loss of stock or damage to the actual forklift if it occurs during lifting operations.
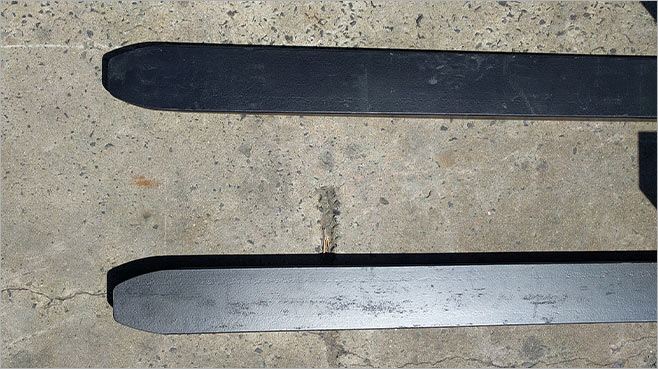
2. Straightness of Blade and Shank
The straightness of the upper face of a tyne’s blade and the front face of the shank shall be checked. If the tyne deviates from the manufacturers design and specifications by more than 0.5% of the length of the blade or the height of the shank, the tyne must be removed from service.
If the blade and shank angle deviate too far from the manufacturers design, this can greatly affect lifting operations as loads may be carried whilst incorrectly balanced against a load guard which could result in a load falling off the tynes.
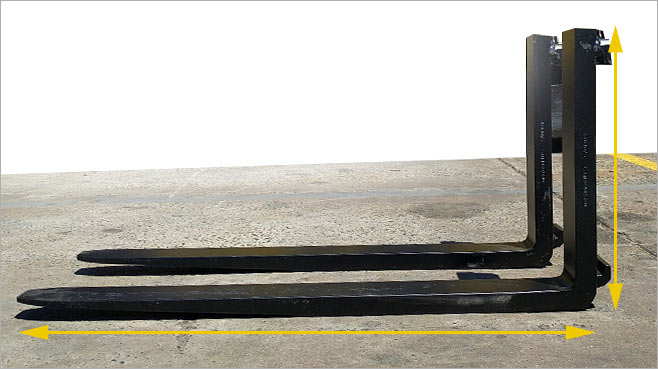
3. Fork Angle (upper face of blade to load face of shank)
Tynes that deviate greater than 3 degrees from original manufacturers design and specification must be replaced and not returned to service.
Like above with the tyne straightness an enlarged fork angle may impact lifting operations resulting in unstable loads being transported.
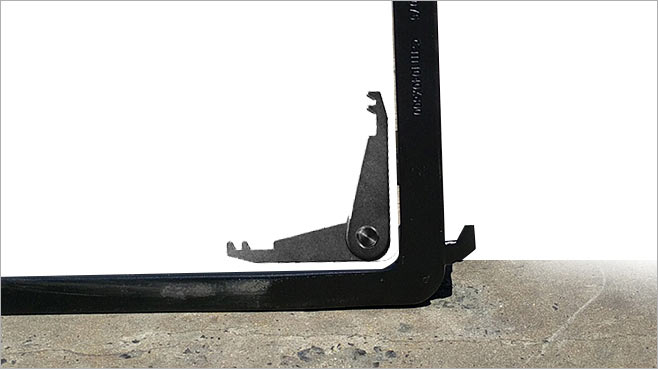
4. Difference in Fork Tip Heights
A pair of tynes should always be approximately the same height as they are installed in pairs and utilised for the same amount of time. If the fork tip height between a pair of tynes exceeds 3% of the blade length, the tynes need to be removed from service.
If tyne tips are of a different height this may adversely affect their lifting ability and lifespan. A tynes load capacity is always halved across the pair of tynes. If one fork tip is higher than the other this may place undue pressure on the higher tyne as this supports loads earlier due to its extended height. Having a full load on one tyne may lead to it breaking or demonstrating signs of stress.
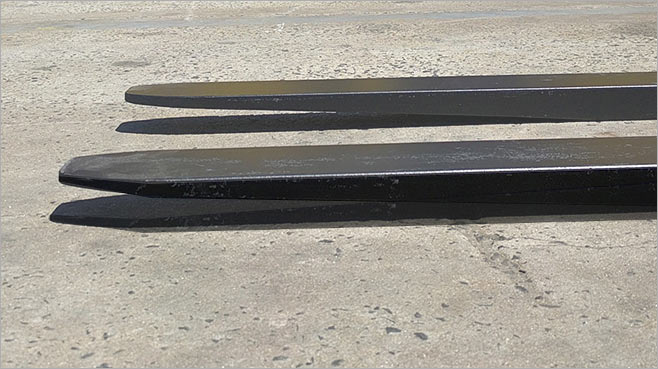
5. Positioning Lock
It is imperative that a tynes positioning lock mechanism works 100%, if there is any defect in this it may result in tynes breaking away from the forklift cage during operations. This scenario could potentially have severe impacts on operator and employee safety as well as implications for the load being carried (i.e. load may fall off tynes).
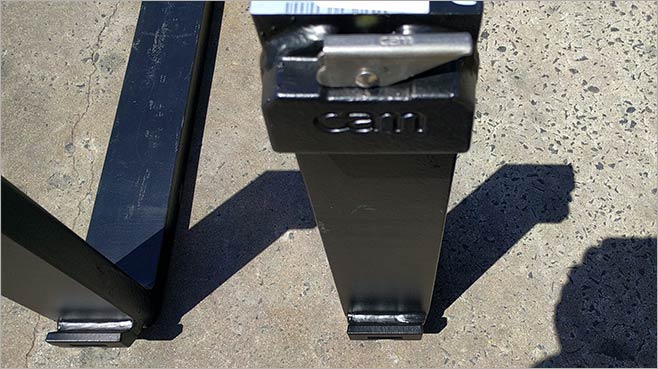
6. Wear
The fork blade and shank need to be thoroughly checked especially near the heel, if thickness is reduced by 10% of original thickness the forks shall be removed from service.
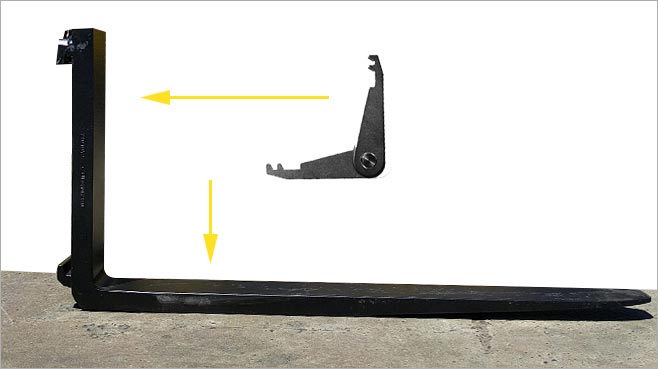
7. Legibility of Markings
If any original manufacturer marking on the tynes are not clearly legible they must be renewed by the original supplier. Markings can include safety and tyne information.
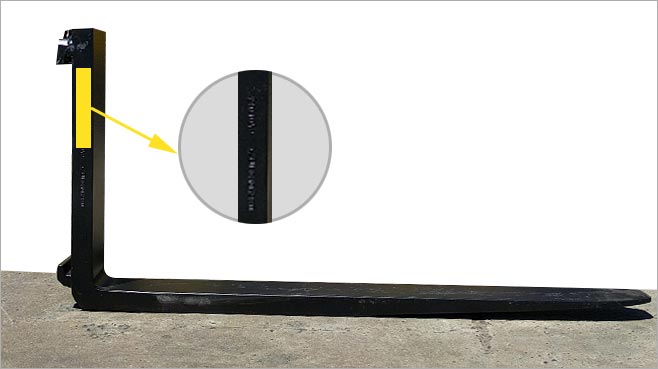
This week’s blog has outlined the seven key elements to inspect when conducting a tyne inspection.
Adaptalift is able to meet all tyne needs through our nation-wide aftermarket service and parts programs. Our fully trained and equipped service technicians are able to conduct tyne inspections both in workshop and at customer sites. Our parts departments are able to provide a comprehensive range of new and replacement tynes to suit any application.
For all your tyne inspection and maintenance needs don’t hesitate to contact us.