Ergonomic Scissor Lift Tables – Improving Worker Safety
Warehouse workers are often required to pick or put away stock on a repetitive basis.
The repetitive motion of bending down to pick-up stock from the floor to then put away on shelves is a common source of worker injuries including back and muscle strains.
To assist in the prevention of worker injuries Adaptalift recommend warehouses invest in and prescribe workers use scissor lift tables.
This week’s blog provides a brief overview of scissor lift tables, their benefits and a list of basic do’s and don’ts.
What is a Scissor Lift Table?
A scissor lift table is a mechanical or hydraulic scissor lift with a flat table surface on top.
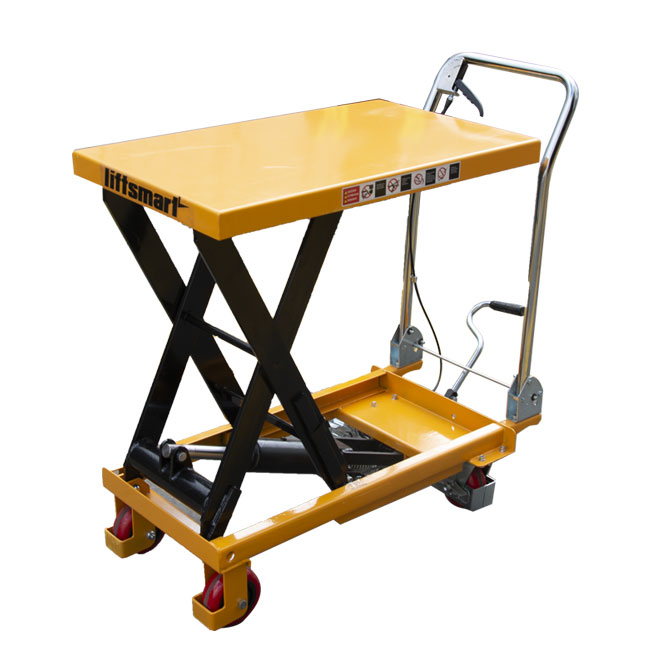
Some models such as those sold by Adaptalift Group are portable as they are on wheels.
Scissor lift tables can come in a variety of capacities ranging from 150kg to 500kg, these are the amounts of weight that the unit can safely lift as part of normal operations.
Depending on the type of table it could be one of three types:
- Mechanical – uses a crank to raise the table
- Airbag – uses an airbag to raise the table
- Hydraulic – uses a hydraulic piston to raise the table
Scissor Lift Table Uses
Typically scissor lift tables are used in warehouse environments but they can also be used in other environments such as mechanic garages and manufacturing plants both indoors and outdoors.
The main benefit of using lift tables is they speed up and simplify the moving of stock and/or products.
Tables lessen the likelihood of workers injuring themselves whilst repeatedly bending down and picking up stock from the ground to then be put
away.
Workers can lift up a box of stock once from the ground and place it at waist height on the raised scissor table lessening the distance they need to bend to pick-up the stock for put away.
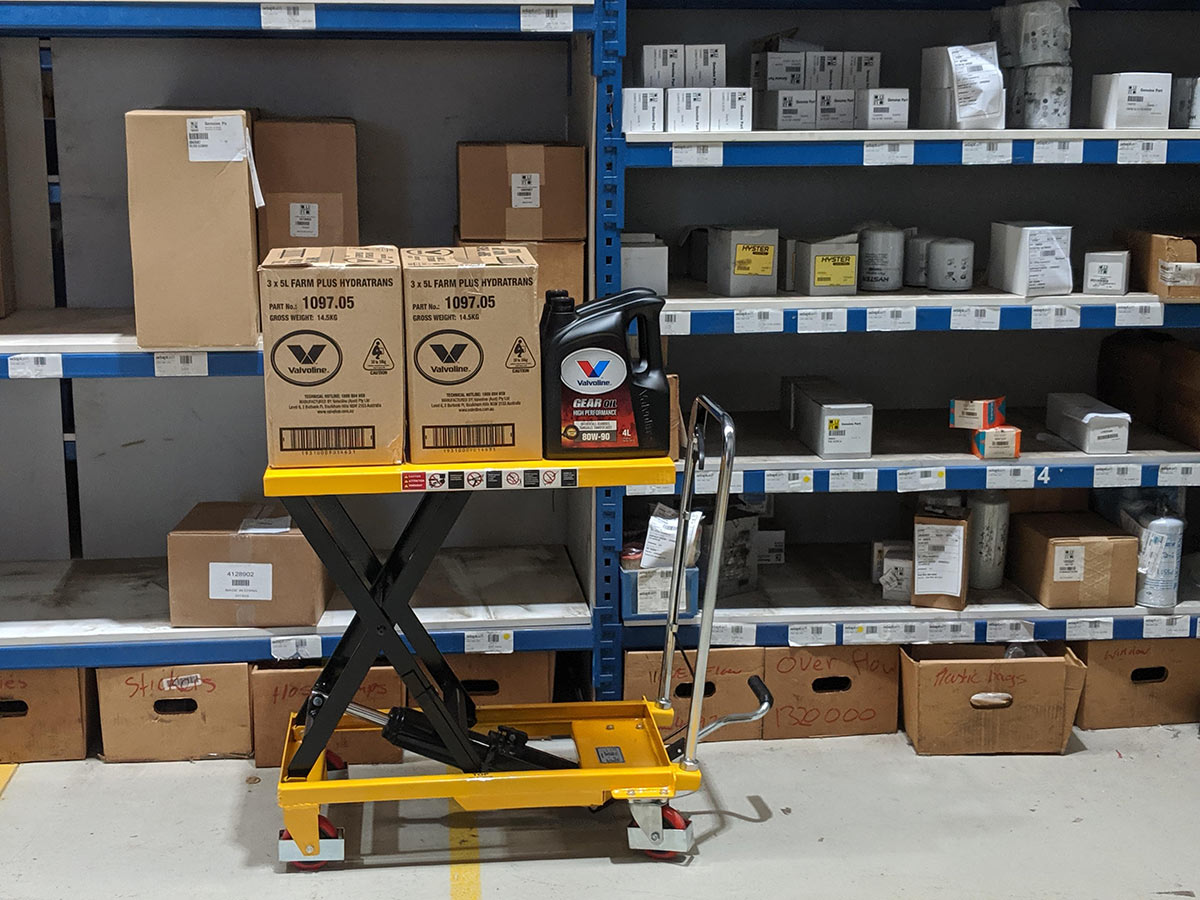
By having stock positioned easily within reach, restocking can also be spend up as workers aren’t constantly reaching down to the ground or even having to climb up and down ladders to put stock away in high up locations.
Scissor Lift Table Do’s and Don’ts
By following the simple list of do’s and don’ts below ensure tables are utilised correctly and workers are kept safe:
- Do select the correct lift table for your application. Make sure the lift capacity can handle specified loads to lift and that the table lifts up to ergonomic hip height of those using it
- Do make sure workers utilise lift tables wherever possible. They are an inexpensive aid that greatly improves employee safety when compared to the cost of workers compensation for injury
- Do locate tables in common areas where floor level stacking and sorting operations occur frequently
- Don’t use a lift table as a pallet jack. Tables are often not rated to lift capacities that pallet jacks are rated to. If they are overloaded you risk breaking the table and also spilling and possibly damaging or breaking product
- Don’t overload the trolley beyond its rated capacity If they are overloaded you risk breaking the table and also spilling and possibly damaging or breaking product
- Don’t use the table as a ladder, misuse like this can lead to serious injury
Adaptalift Group stock a wide variety of scissor lift tables with lift capacities from 150kg.
To view our range of tables visit our online store or to speak to a team member regarding your materials handling needs contact us on 13 22 54.