12 Ideas to Improve Warehouse Safety
1. Have a designated smoking area away from gas and other hazards
Warehouses may contain a wide variety of flammable liquids and gases such as LPG gas cylinders.
To ensure the highest level of warehouse safety around these dangerous sources of ignition it is imperative all potential sources of fire are kept far away.
The easiest way to protect a warehouse is to establish and enforce a designated smoking area that is positioned well away from all sources of ignition.
Any person whether employee, supplier or visitor wishing to smoke must do so in this designated safe zone to ensure errant cigarette butts or lighters cannot ignite a fuel source causing a potentially fatal explosion.
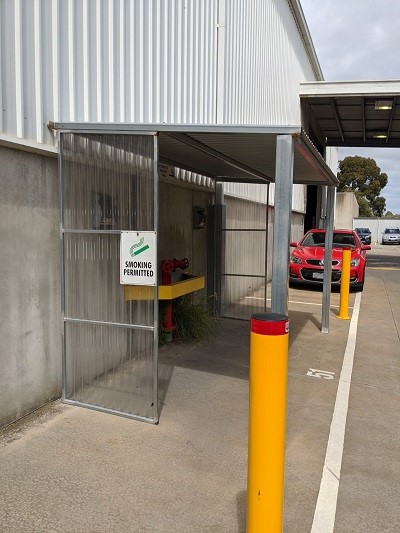
2. Ensure a strong personal protective equipment policy (PPE policy) is adhered to
There are a number of hazards for employees who work in warehouses.
To ensure employee protection it is imperative a strong personal protective equipment policy (PPE) is adhered to.
All employees must wear PPE provided to them by the company at all times they are working in the warehouse.
Items that employees need to wear as part of a PPE policy may include:
- Protective footwear – to protect employees feet from being run over by machinery such as forklifts or from heavy falling objects
- High visibility clothing – to ensure employees are clearly visible to machinery operators and other employees, high vis clothing must be worn to make people stand out from the surroundings. When working at night high visibility clothing must also have reflective tape
- Protective eye-wear – must be worn by operators of machinery that generate sparks, projectiles or dangerous chemicals become airborne to protect employees’ eyes from damage.
- Employees involved in regular lifting or lifting of dangerous items need to wear gloves to protect their hands
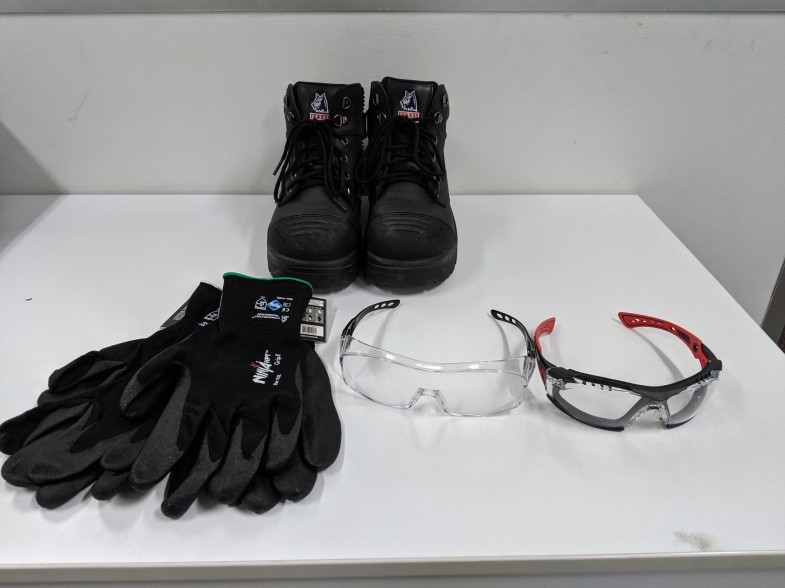
3. Appoint qualified first aid wardens
All warehouse facilities should have multiple first aid wardens, individuals who have attended advanced professional first aid training and hold up to date certification.
In the event of a medical incident or emergency first aid wardens are first responders that can take charge of the situation, assess injuries and provide potentially lifesaving treatment until emergency services arrive.
It is imperative that first aid wardens are promptly replaced when one leaves a business.
They should also ensure their certification is maintained via refresher courses before the expiry of their current certification.
4. Appoint qualified fire wardens
Like first aid wardens and particularly pertinent for warehouses housing flammable or dangerous chemicals qualified fire wardens must be appointed.
Wardens will have completed training and hold up to date certification.
In the event of a fire they will take charge of the evacuation of all staff.
Fire wardens need to be immediately replaced when one leaves a business
5. Ensure first aid kits, hazardous waste spill kits and emergency medical stations with showers and eye rinsing equipment are setup
It is imperative that first aid kits are correctly stocked and available in all parts of a warehouse for employees to utilise in case of injury or emergency.
For warehouses storing and handling dangerous goods hazardous waste spill kits and emergency medical stations with showers and eye rinsing equipment are installed.
Emergency spill kits assist in the containment and clean-up of hazardous chemical spills, whilst showers and eye rinsing stations are there to treat employees if they become affected by chemicals.
6. Ensure you have effective signage and warnings
It is imperative in any warehouse that signage is displayed correctly.
Types of signage necessary to display include (but not limited to):
- Signs warning of danger
- Designation of specific areas within a warehouse
- Speed limits
- Traffic flow guidance
In all cases signage must be clear and unambiguous.
Employees must know upon sighting the sign what it means and what they need to do to obey the signs direction.

7. Design and implement a warehouse traffic management plan to safely separate plant and equipment from pedestrians
Powered mobile plant moving around warehouses reversing, loading and unloading are frequent causes of employee injury and fatalities in the workplace.
One way to prevent collisions and injuries between employees and plant equipment is to implement a traffic management plan.
The plan will have distinct separate areas for pedestrians and mobile plant equipment to move in, the physical separation lessens the chances of injury.
8. Replace Hand Pallet Jacks with electric pallet jacks to reduce the risk of operator injuries
Manual handling of heavy loads in a warehouse heighten the possibility of employee injury.
Manual hand pallet jacks with a maximum lifting capacity of 2.5T when fully loaded require a large amount of force to move and slow down the load.
To assist stock movements semi and fully electric hand pallet jacks can be utilised.
These motorised units greatly assist in the easy movement of heavy loads, they also assist with braking preventing loads from becoming out of
control and potentially injuring operators or damaging stock or capital equipment.
9. Enforce a 3 meter safety rule (pedestrian free zone) around all plant and equipment
In mixed traffic warehouses where mobile plant equipment operate alongside employees a 3 meter exclusion/safety area around all plant and equipment.
All employees operating in a warehouse must be informed of and adhere to the safety exclusion zone to lessen the chances that they will be injured.
The 3m exclusion zone should be accurately and visibly signed to remind all employees through signs in the warehouse and warning stickers on plant and equipment.
10. Ensure your forklifts are safety checked and maintained daily via daily checklists
To ensure your forklifts are safe for operations, daily safety and maintenance checks should be conducted at the start of each shift.
These checks will look at common components and functions to ensure they are operating optimally.
Any unit that fails a pre-start safety and maintenance check should be removed from operation until they are assessed and repaired by a qualified technician.
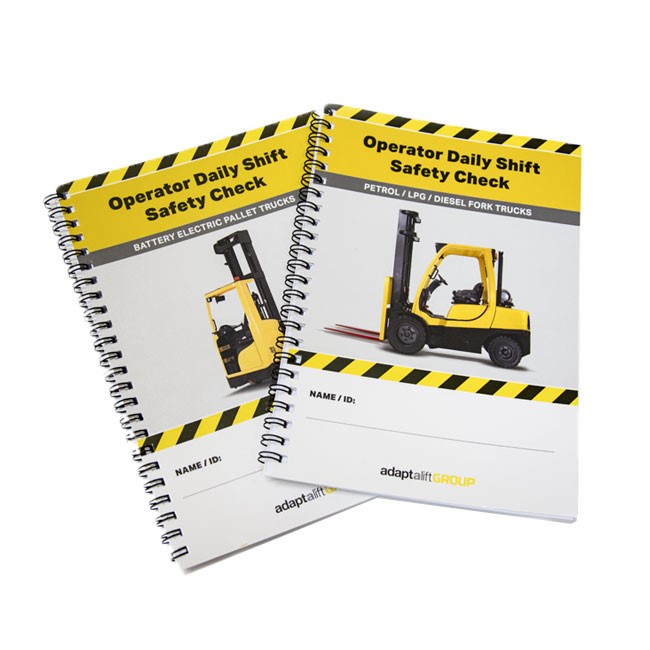
11. Ensure any fault units are immediately removed from operation till repairs have been made by a qualified technician
When a unit fails a safety or maintenance check as conducted above the unit needs to be immediately removed from operation till it can be assessed and repaired by a qualified technician.
To ensure the unit is not operated until repairs have been completed a lockout tag must be installed on the unit detailing the following:
- Date the fault was detected
- Type of fault
- Any action needed
- Name of technician who has locked the unit out of use
The lockout tag can only be removed once the unit has been correctly repaired by the named technician on the tag.
12. Ensure all forklift and mobile plant operators are certified and hold the correct license
All operators of forklifts and equipment must have completed the correct training and hold the required valid license.
Operator licensing measures can be installed where operators much present a credential cards showing they hold a valid licence to operate the unit on their shift.
The controls will not allow an unlicensed operator to utilise machinery.
Fleet management software such as ForkTrack can send reminders to management of upcoming licenses that need renewal ensuring that licenses do not expire.
For more information regarding warehouse safety or any of the products outlined in the aforementioned safety tips contact us on 13 22 54 or email us.