Key Factors that Affect the Average Lifespan of a Forklift
The lifespan of a forklift is calculated and measured by the number of hours it has been operated for.
Whilst there is no hard strict number of hours a forklift should operate across its operational life a number of manufacturers suggest that most forklifts average operational life is between 10,000 to 12,000 hours, or 5-6 years of 8 hours a day operation.
In this post we briefly examine some of the key factors that directly impact on the lifespan of a forklift, including:
- Fuel type
- Operator behavior
- Work environment
- Maintenance practices
Fuel Type
In recent years battery electric forklifts have begun to overtake internal combustion units as the most common types of forklifts being purchased.
A significant reason for this increase popularity is battery electric forklifts extended operation lives compared to IC units.
With fewer moving parts in battery electric forklifts there are fewer things that can go wrong along with reduced maintenance costs can lead to longer operational lifespans.
Whilst common parts such as tynes, tires and lift chains must be replaced as part of routine maintenance on all forklift types battery electric included, electric forklifts typically only need their battery replaced at the end of its life.
On average a new battery is required to be installed every 5 years.
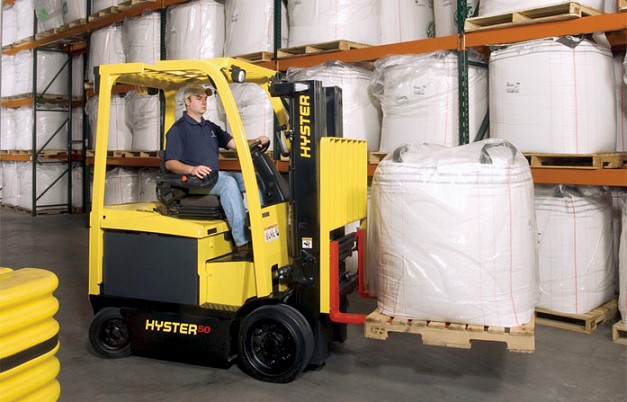
Operator Behavior
Operator behavior can have a large impact on a forklifts operational lifespan.
Negative behaviors such as aggressive driving, careless operation and inattention or negligence can greatly reduce the operational life of a forklift.
An example of how negative operational behavior can affect a forklift is speeding, whilst being driven at excessive speeds the unit’s mast, drive axles and overhead guards are susceptible to costly impact damages if the driver loses control at speed and a collision results.
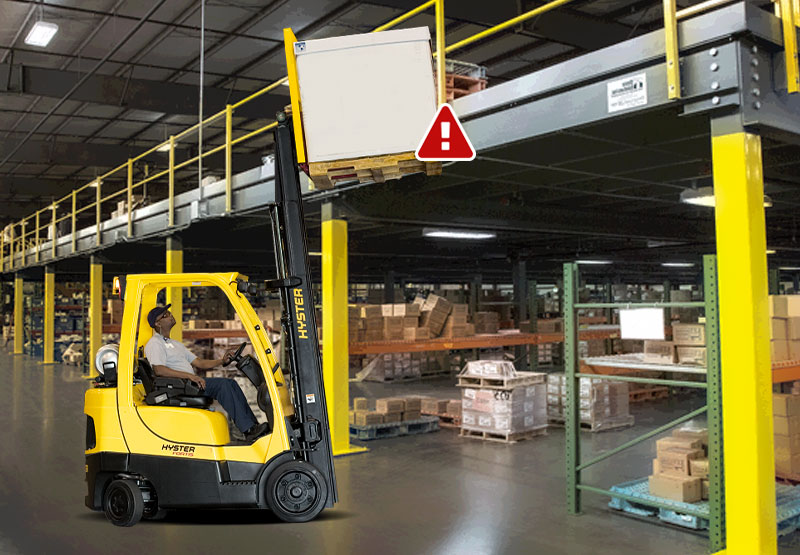
As well as operating the forklift safely within its limits it is important operators conduct pre-shift inspections of the unit to detect and rectify any problems before it is potentially operated whilst unsafe.
A major part of pre-start inspections includes the operator checking the levels of important oils such as engine and hydraulic oil.
Failure to have the correct levels of engine oil can irreparably damage the engine, which will likely mean the whole unit will need to be replaced.
Controlling forklift operator behavior can be hard for companies, however in-depth operator training programs combined with telemetry and safety system such as ForkTrack can greatly assist ingraining good behaviors into operators.
Some features of ForkTrack’s safety system that assist operator behavior include:
- Speed limiting controls the maximum speed the operator can drive the forklift at
- Detect, record and alert management to any instances of a collision that may damage the forklift
- Pre-start checklists ensure operators complete the checklist each time before they begin operating the forklift
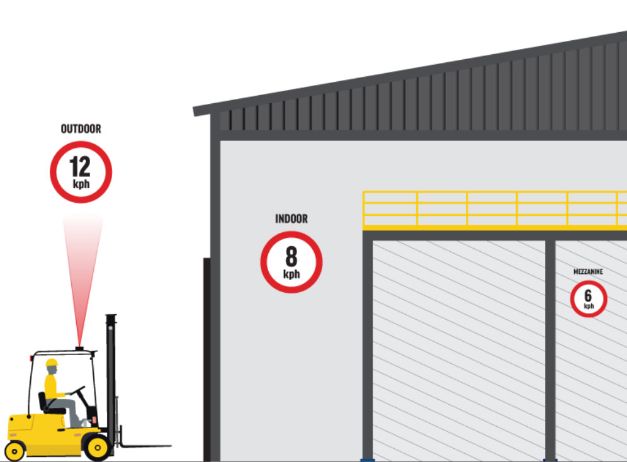
Work Environment
Forklifts operate across a wide variety of environments, however all operating environments aren’t equal.
Some examples of the different environments include:
- Outdoor construction sites with uneven ground and exposure to weather such as rain
- Dirt and debris filled areas such as recycling plants or agriculture product processing plants
- Cold storage facilities with extreme cold temperatures
- Chemical plants with dangerous and corrosive chemicals
Each of the above example work environments can have a negative effect on a forklifts operational lifespan.
Some common problems may include:
- Locked up drive motors and axles from debris caught in them
- Clogged cooling systems from dust and debris buid-up
- Rust from exposure to rain and moisture
- Corroded electrical systems from rain ingress
Some simple ways to improve a forklifts work environment to improve longevity include:
- Keep the unit clean and dry to limit the growth of rust
- Regularly remove debris and dust build-up by blowing out the unit with compressed air
- Cover all exposed wires to limit water ingress and prevent corrosion
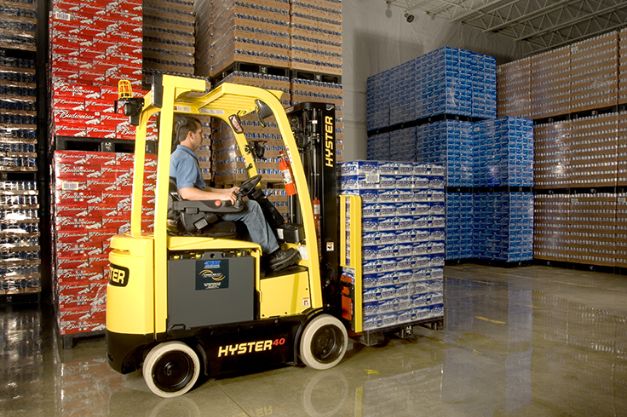
Maintenance Practices
Regular maintenance plays an integral role in extending the longevity and operating life of a forklift.
It ensures the safety and mechanical integrity of the unit.
Without regular maintenance the forklift can become uncomfortable and dangerous to operate.
All manufacturers recommend maintenance at regular intervals throughout a forklift operational life.
Some companies struggle to keep up with regular maintenance across their fleet which is why Adaptalift Group offers scheduled maintenance plans to all our customers to maximise the lifespan of their forklifts.
Scheduled maintenance carried out by one of our highly qualified technicians will keep forklifts in optimum condition, whilst also quickly detect and rectify any issues before they snowball and become serious and expensive.
Committing to a comprehensive maintenance plan for a forklift can greatly extend its operational lifespan.
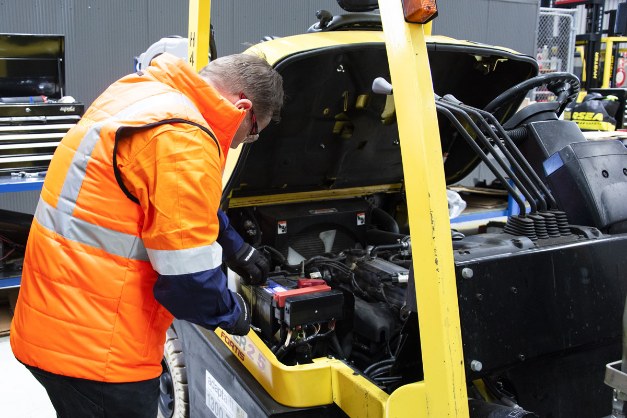
In this post we’ve examined how a forklifts fuel type, operator behaviour, the work environment and regular maintenance can impact the operational life of a forklift.
For more information on ForkTrack safety system capabilities or to find our more about our comprehensive scheduled maintenance plans contact a member of our team on 13 22 54 or fill-out a contact form and we will reply as soon as possible.