Safeguarding Against Operator Fatigue for Forklift Operators
Operator fatigue in the forklift industry refers to the state of tiredness, weariness, or sleepiness that can impair a forklift operator’s ability to work safely and effectively.
In the workplace, this is a significant concern due to its potential to cause workplace accidents and injuries.
What Contributes to Operator Fatigue?
Various factors can lead to worker fatigue, including, inadequate sleep, long work hours & stress.
In the context of forklift operation, noisy environments, uncomfortable/bumpy riding surfaces, and poor ergonomics can exacerbate fatigue.
To better identify driver fatigue here are some signs to look out for:
- Inability to focus
- Lack of awareness of surroundings
- Making frequent mistakes
- Blurred vision
- Muscle soreness or weakness
- Irritability
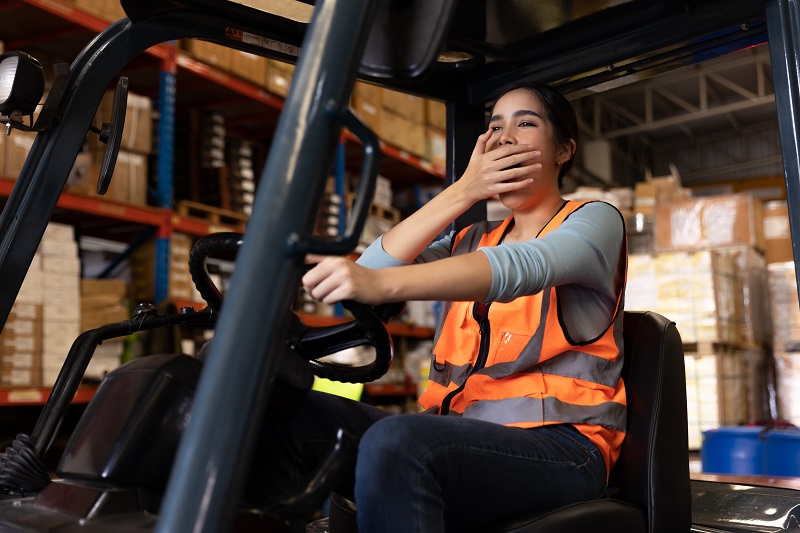
Employers have a responsibility and duty of care to ensure that the equipment provided to operators is comfortable and easy to use.
Impact of Fatigue on Forklift Operator Safety
Fatigue poses a significant risk in the workplace, impacting decision-making, communication, attentiveness, and alertness.
Recognising signs of fatigue in employees is crucial to safeguard the well-being of themselves, colleagues, and the company.
Establishing open lines of communication fosters a safety-oriented culture and enables timely intervention when fatigue is detected.
High noise, work environments such as manufacturing facilities and busy warehouses, can present several challenges.
A driver might not hear a co-worker issuing a warning, or they may fail to notice unusual noises from the forklift.
This can result in the consequences of a single accident, such as a collision between two forklifts, which can be severe.
Such incidents have the potential to disrupt operations, leading to delivery delays and financial losses.
Therefore, it’s imperative to promptly address any injuries sustained by forklift operators, prevent further complications, and conduct thorough equipment inspections to identify and rectify any damage or issues.
What are Employer’s Obligations?
Employers are obliged to:
- Identify workplace hazards (e.g. noise, slippery surfaces, and working at heights).
- Assess the risks posed by these hazards (e.g. risk of tripping or falling)
- Take steps to eliminate or minimise these risks
These responsibilities ensure the safety of forklift operators and pedestrians in the warehouse, ultimately mitigating operational disruptions and productivity losses.
There are guidelines provided by the National Employment Standard (NES) and gov.au that define that a full-time employee should not be working any more than 38 hours a week (unless their award or enterprise agreement specifies different hours) or if an employer asks them to work reasonable extra hours.
For an employee other than a full-time employee, the lesser of 38 hours or the employees agreed ordinary hours for the week.
For forklift usage, there is no set limit to the number of hours you can operate a piece of machinery for.
However according to Safe Work Australia, a person who operates a forklift must hold a high risk work forklift licence.
Only the individual who has both the right licence to perform the high risk work and suitable workplace experience may operate the unit.
Strategies to Mitigate Forklift Operator Fatigue
Addressing operator fatigue requires collaborative efforts and recognising that that a one-size-fits-all approach may not effectively minimize fatigue in the warehouse.
Each employee may have different concerns or reasons for experiencing fatigue.
Therefore, implementing a tailored approach will identify specific challenges contributing to fatigue by:
- Encouraging dialogue with employees to identify specific challenges
- Providing noise-cancelling headphones,
- Adjusting sleep schedules
- Improving lighting
- Promoting ergonomic practices to alleviate physical and mental strain.
- Ensure accessibility to support resources
Extended breaks are another effective method to address operator workplace fatigue, but it’s essential to adhere to laws regulating break frequency and duration.
Additional breaks may be necessary if employees are running out of energy.
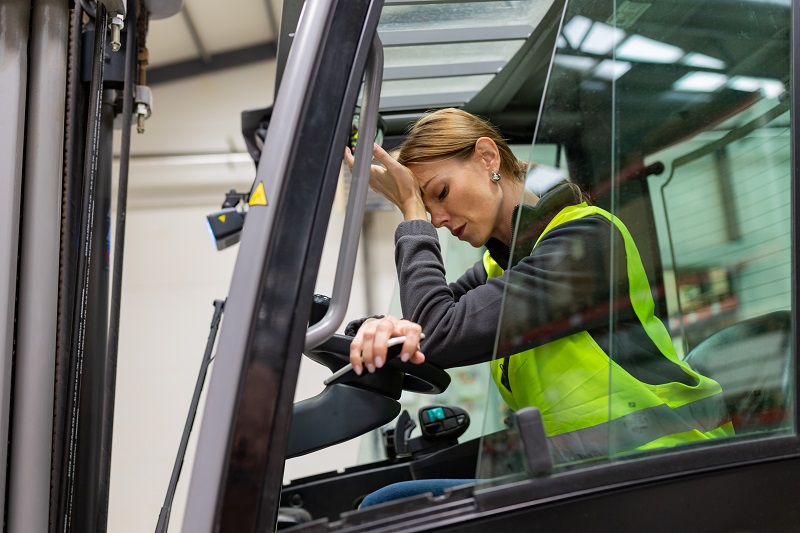
In safety-critical environments like warehouses, fatigue can impair focus and increase the risk of accidents, particularly for forklift drivers.
Prioritise employee breaks to enhance assertiveness, productivity, and safety standards.
Consideration of the workplace layout and conditions is also crucial to minimise accidents and promote focus.
Improved visibility and workplace design can enhance safety and productivity.
Addressing blind spots and pedestrian-vehicle interaction areas reduces the risk of accidents. Implementing areas for forklift parking, low-speed zones, and pedestrian exclusion areas, along with implementing clear marking signs and warning systems, further enhances safety.
Incorporating additional safety measures such as visual warning devices like the Artificial Intelligence Vision Assist’ (AiVA) System can increase operator situational awareness by automatically detecting and advising when pedestrians approach forklifts contributing to a safer work environment.
Addressing operator fatigue in the warehouse is essential for ensuring workplace safety, productivity, and employee well-being.
By implementing tailored strategies can effectively minimise fatigue-related risks.
Recognising the individual needs of employees and fostering a culture of collaboration is the key to successfully reducing operator fatigue and creating a safer work environment for all.