Adaptalift Hyster and AET improve productivity and reduce downtime at Coca-Cola Amatil
Adaptalift Hyster recently collaborated with Coca-Cola Amatil (CCA) on a project to modify CCA’s battery room at their Eastern Creek site in New South Wales. Adaptalift Hyster has been supplying CCA’s materials handling solutions for over a decade.
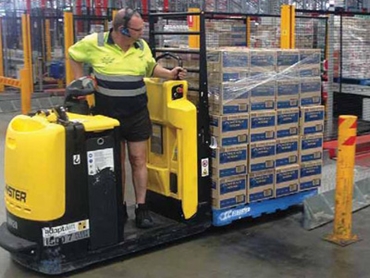
Applied Engineering Technologies (AET), a subsidiary of Adaptalift Hyster that specialises in the integration of telemetric devices into industrial and consumer equipment categories, also played a key role in the CCA battery room modifications.
The enhancements to the battery room included a reconfiguration in order to accept the Hyster L02.0 batteries, fitting of an automatic watering system and a battery queuing station. Each battery was also fitted with a specialised battery monitor to allow real time web based reporting. The battery room modifications would ultimately provide the site with increased operational productivity while minimising any downtime.
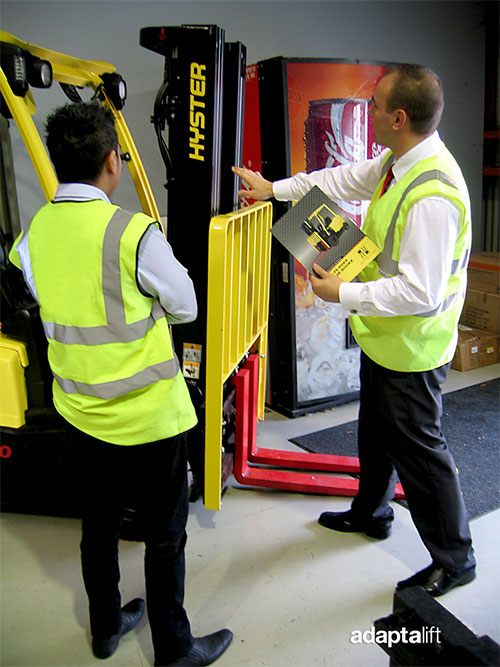
CCA’s Eastern Creek facility, which was launched in 2011, uses injection moulding technology to manufacture plastic bottle caps and PET resin preforms, which are test-tube shaped moulds used to manufacture PET plastic beverage bottles. Terry Davis, CCA’s Group Managing Director explained that the facility would help them deliver on their goal to develop the most efficient and customer-centric fast moving consumer goods supply chain in the country. The efficiency requirements at this site were therefore at the forefront of the battery room enhancement project.
Adaptalift Hyster installed 27 new compact high frequency battery chargers onto multi-shifter battery bays, which have significantly enhanced operations. Jon Burton, Warehouse Shift Manager of CCA explains that the battery chargers make operations a lot smoother.
All multi-shifter battery bays in the battery room at the site were reconfigured to accept the Hyster L02.0 batteries, and 27 new Hyster L02.0 low level order pickers to upgrade the previous fleet with second shift batteries complete with single point watering systems were delivered. The Hyster low level order pickers are being used for case picking at the site.
Burton said that the equipment was reliable and when breakdowns occurred, an onsite Adaptalift Hyster technician was able to fix the problem with relatively little downtime. Each new charger was fitted with automatic watering solenoids at the site. This unique watering system allows for batteries to be automatically watered at the completion of each charge cycle, eliminating the need for operators to manually water the batteries on a regular basis, thus contributing to the safety effort of the site’s operation.
The battery queuing station installed into the battery room at CCA alerts the operator of the next battery ready to be swapped into the next machine. This unit has an LCD display board along with a visual display header on top of each charger, which signals a bright LED blue light when a charger has the battery ready for the next change. A chime sounds if the correct battery is picked or a siren and a recorded voice alert the operator if the wrong battery is picked.
Each battery has also been fitted with a specialised battery monitor to monitor and record information about the battery in real time, including the number of cycles, how deeply the battery is discharged, how the chargers are performing as well as ensuring batteries have sufficient water.
Instead of changing batteries every shift, the batteries are only charged when required, which increases the life of the batteries and has a positive effect on productivity. Eliminating the need for a battery change at the beginning of each shift allows operators to minimise downtime and increase their work capacity.
Advancements in technology allow both the queuing station and the battery monitors to provide reporting over the internet using a modem and cloud-link system to download the information. This information is updated to a website allowing the operation to be viewed remotely at any time. The innovative management solution of the battery room powered by AET is another contributing factor to increasing the productivity for the site.
The modifications executed by Adaptalift Hyster along with AET at the CCA Eastern Creek site have not only enhanced the operations at the facility but also provided world leading technology to manage the operations and improve overall output capabilities.